More than 100 years committed to technical progress has made us the leading manufacturer in the fields of variable AC drives, servo drives, control technology and robotics.
Cobot Palletizing: How Unilever uses cobots to relieve strain on employees in the palletizing process
Short-term restructuring measures at Unilever's Heilbronn site involved the maintenance of a large palletizing station. Instead of additional staff, cobots were used for the first time - for a period of one week using a practical rental model. However, flexibility was only one of the many advantages from which the plant benefited.
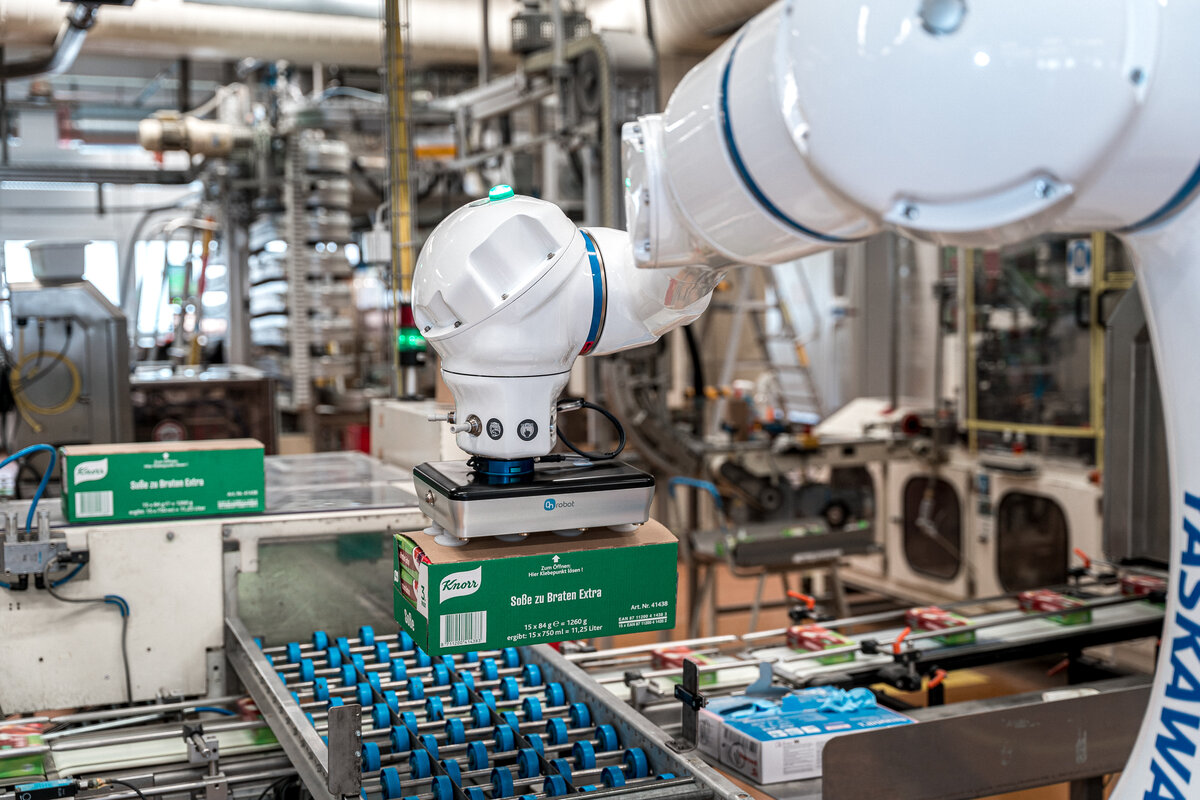
"We attach great importance to actively managing our employees’ health," says Michael Schenk, explaining the first use of cobots in his company.
He is a master industrial electronics technician at the Unilever Knorr plant in Heilbronn and is responsible for technical issues within the company.
"That’s why we are fundamentally concerned with the topic of ergonomics, especially in the area of palletizing," he adds. "We saw the cobots as an opportunity to effectively relieve the strain on our employees".
The introduction of a new stretcher meant that one of the plant's large automated palletizing stations had to be shut down for a week. This circumstance was also used for maintenance purposes, but it also meant that the finished packs now had to be palletized by hand. While in the past this was done by relying on additional personnel, project engineer Thomas Bittner, who specialises in automation projects at Unilever, decided to use cobots for the first time in spring 2023.
"At that time, we had already repeatedly considered the question of whether using cobots would pay off for us," he says. He adds: "However, because the monetary expenditure for this is quite significant, we hesitated for a long time. But when we became aware of Bayer's cobot rental model in connection with our plans to introduce the new stretcher, we jumped at the chance of testing it in operation and with virtually no risks involved".
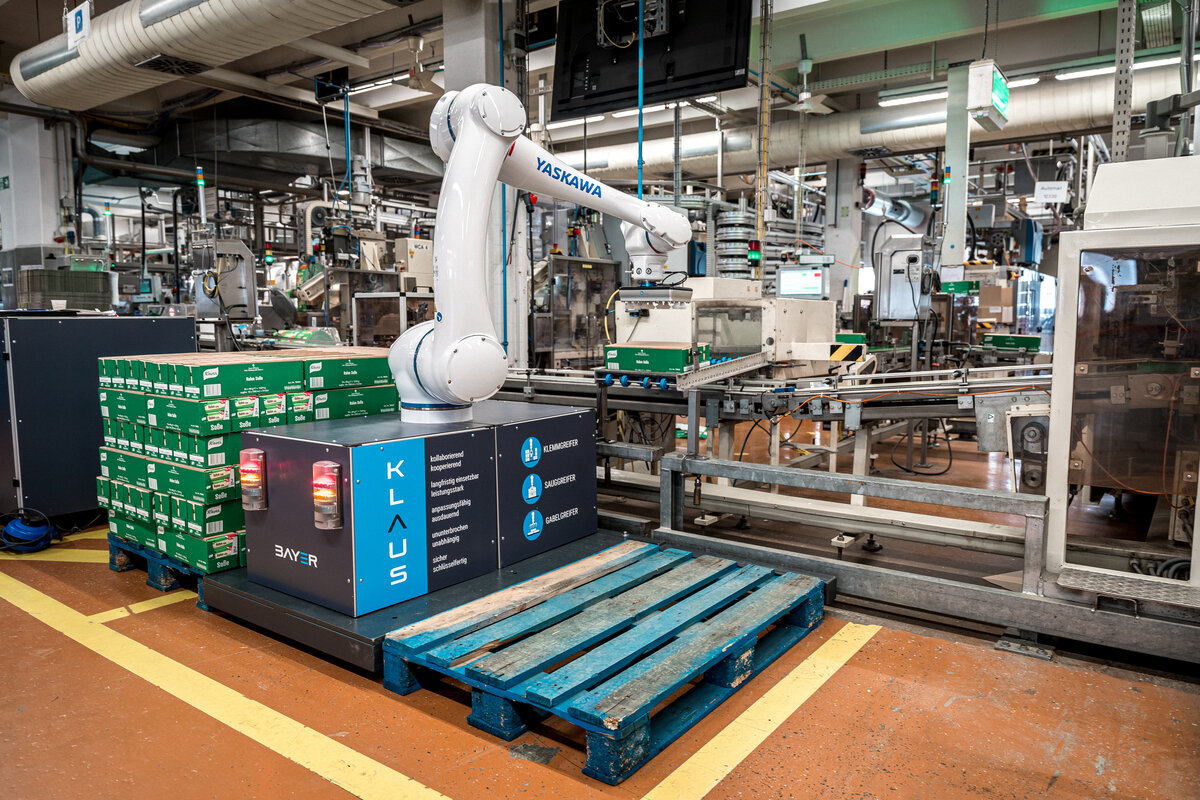
Ergonomics and operational safety are very important
There are filling machines and cartoning machines located in the area of the affected palletizing station. The packs produced here are fed via a conveyor belt to the central palletizing system and then as finished pallets to the high-bay warehouse. If the automated process changes, for example due to maintenance or if a new machine is installed, certain processes must be carried out by hand during this period. In this case, this meant that on some lines the packs had to be set down manually: the responsible employees pick up the packs by hand, place them on the pallet and another employee transports them with an electric lift-truck to the docking system, from where they then go to the high-bay warehouse.
"If you have to set down packs like this for eight hours, your body really lets you know what you’ve been doing all day in the evening," says Bittner. "That's why it was important for us to relieve the strain on our employees through automation. And thanks to the cobots, we were successful".
In order to implement the project, Bittner brought the automation specialists of Bayer GmbH & Co KG from Wörnitz in Franconia on board. In addition to the currently unique offer of being able to rent the cobots for a limited period of time, the decades of experience of Bayer engineers in the field of automation and the fact that they were located nearby, were important factors in coming to a decision.
"Especially as this was the first time we used cobots, which work hand in hand with our team and without a security fence, it was important that the service provider could get to us within a very short time," says Bittner. In addition to ergonomics, the topic of operational safety is also very important at the Unilever plant in Heilbronn.
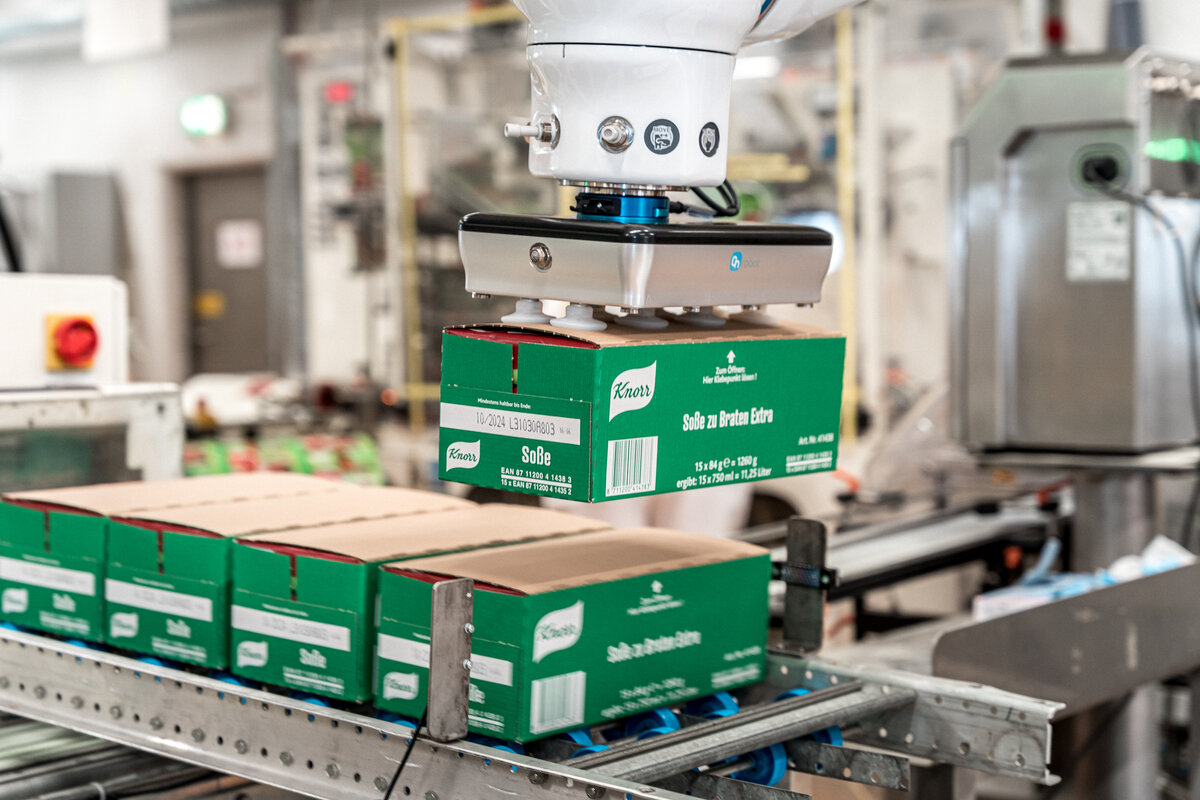
Maximum security thanks to experienced service provider
Since Unilever had no experience with cobots at that time, the Bayer engineers provided a video-based introduction and also explained the safety criteria and standards according to which cobots are used. The main focus is on the ISO 15066 guideline for safety requirements for collaborative industrial robot systems and the working environment.
Unilever decided to place the order - and after just four weeks, the cobots were ready to go. In general, it’s the issue of safety which is one of the main reasons why many companies hesitate to use cobots. There is a lack of practical experience with this relatively young technology. Experienced suppliers such as Bayer therefore usually offer a risk assessment at a very early stage of the project, based on examples, if necessary even as part of an on-site inspection. In addition, an external expert for cobot safety is also consulted on the project in individual cases - an experienced specialist who, like Bayer GmbH, is a member of the German Robotics Association.
However, before the cobots were delivered, the plant's safety department was involved in the project and informed at an early stage about how the cobots would work. So was the plant, division and production management, the shift coordinators and the employees in the palletizing stations concerned, the majority of whom followed the project with great interest and even enthusiasm. Schenk, the project implementer, commented: "Nobody was worried that the cobot would take away jobs. And there is no reason to worry because the cobot really only does the unpleasant work and there are many other tasks to be done besides setting down pallets. In the end, everyone was happy that KLAUS had done all the heavy lifting so well".
The positive internal risk assessment by the plant and production management as well as the force measurement and a test run before the cobots were put into operation finally removed the last concerns the safety and area managers still had.
Cobot "KLAUS" needs no compressed air
A total of two Bayer cobots of the "KLAUS” type (mounted on a basic model from Yaskawa) were installed at Unilever, the frames of which were also provided by Bayer on a rental basis. The unique selling points of the cobot - the integrated air lines that make compressed air superfluous - did not play a role in the Unilever project. In many other applications, however, the situation is different, as packs are often picked up by vacuum with the aid of a suction cup. In Unilever's case, however, the packs were picked up purely electrically via a third-party robot gripper. The gripper was selected by an experienced Bayer engineer in such a way that no expensive compressed air had to be used. And since it is a standard product, it could also be delivered right away - another advantage given the tight time frame.
The installation was carried out at four filling stations and two case packers of the central palletizing system. While three packs were put together at one station, two packs were assembled at the other. Work is normally done in three shifts, so the cobots took over the work of six potential employees during the one week that the palletizer was shut down.
Since the pusher normally responsible for the onward transport of the finished packs had been shut down together with the central palletizing system - and Bayer itself was unable to provide a conveyor belt within the tight time frame - two flexible roller conveyors were installed by an external service provider, on which the packs were each fed to the cobots in a centred manner. Centring plays a key role with regard to saving time. If it is accurate, the cobot only has to pick up the packs and not move them back and forth to reach them. Even more time was saved by having each of the two cobots working at two pallet positions. In this way, when one pallet was finished, everyone just had to switch to the other side to continue working without interruption. In the meantime, the finished pallet was taken away by an employee.
Challenge and project evaluation
Before commissioning the two cobots, Unilever had provided the Bayer engineers with palletizing diagrams, product dimensions and information on the technical plant and the cobots were already programmed in advance based on this information. One challenge was the desired cycle time within which the cobot had to pick up the packs: one piece every ten seconds. It was possible to approximately achieve the desired clock rate, thanks to programming know-how on the one hand, but also by slightly scaling back production on the other. The fact that the desired speed could not quite be achieved was also due to the fact that a double head was originally planned, which could have accommodated two packs at once. However, due to the tight time frame, this could not be implemented.
Nevertheless, Unilever project engineer Thomas Bittner assesses the project highly positively:
"Cooperation was very good and Bayer responded extremely quickly to any wishes we had. We know that the time frame for the overall project was somewhat tight. Together with Bayer, however, we mastered this challenge in the best possible way. We have achieved what we wanted, namely to relieve our employees of a great deal of strain". And Unilever technology specialist Michael Schenk adds: "We quickly realised, especially when fine-tuning the cobots on site, that the Bayer employees know what they are doing. They have a lot of experience and, clearly, the more experience someone has, the faster they get things done. You simply need experts in the machine sector".
On the day of installation, Bayer engineers, specialists from Yaskawa as well as the roller conveyor manufacturer were on site to ensure that the cobots got off to a good start. The people in charge of the project at Unilever also pointed out that the fast response and close cooperation between all those involved were extremely good. And Bittner adds: "We have already worked with system integrators from various automation technology suppliers, and I have to say that Bayer engineers clearly stand out here due thanks to their speed, their expertise as well as their proactive approach."
Conclusion: Using cobots for palletizing at Unilever's Heilbronn plant was so successful that the company is currently considering equipping the two plants that currently still have to manage without central palletizing - and in which the packs are therefore still set down manually - with their own cobots on a permanent basis.
Not least because it is hoped that this will also reduce sick leave in the company. A win-win situation - because the company benefits from lower absenteeism rates and the employees from the fact that their health is being protected.
However, it’s also possible that the rental model could also be used again when the next lot of maintenance work has to be carried out. Because one thing is clear, says Unilever project engineer Thomas Bittner: "The cobots have also brought us a very big step forward internally. Because all the managers were able to see for themselves how well we can integrate a cobot into our operations. We now have a completely new perspective on the subject. This is something we can build on. KLAUS has left a lasting impression."
About Bayer
Bayer GmbH & Co KG is an owner-managed company based in Wörnitz, Franconia, and has been operating as a flexible industrial partner in the fields of robotics, engineering and 3D surveying with state-of-the-art laser scanning equipment since 1999. With around 50 employees, companies from a wide range of industries are supported in implementing their automation projects. From consulting and planning to implementation and final commissioning - and more. Bayer trademark: The "Bayer 360 degree automation system". It includes interlocking know-how, coordinated processes and short development times.
© Unilever/Bayer, 2023
Contact:
Bayer GmbH & Co KG, Industriestrasse 14, 91637 Wörnitz, Germany
Tel: +49 (0)9868 / 98 77-209, Fax: +49 (0)9868 / 98 77-22
Internet: www.bayer-tech.de | www.bayer-automatisierung.de