More than 100 years committed to technical progress has made us the leading manufacturer in the fields of variable AC drives, servo drives, control technology and robotics.
Innovative robot welding cell ensures maximum flexibility
- Industries
- Metalworking
- Applications
- Applications | Arc Welding
- Client
- Arburg
- Products
- AR2010 - AR Series
Solution for lot size 1
The renowned injection moulding machine manufacturer Arburg provides proof that batch size 1 and full automation are not mutually exclusive with a pioneering robot welding system. On the contrary: Such challenges are solved efficiently and economically at the Lossburg headquarters.
Founded as a small business in the idyllic Black Forest in 1923, Arburg achieved a spectacular rise to become one of the world's leading machine manufacturers for plastics processing. The family-owned company currently has around 3,200 employees worldwide and still manufactures exclusively in Lossburg - now on an area of over 170,000 square meters and with an extremely high vertical range of manufacture of around 60 percent.
The high-quality all-round injection moulding machines with hydraulic, hybrid, electric or vertical injection moulding technology are in great demand. An export quota of about 70 percent underlines the international esteem in which these machines are held. The automation technology used to produce them is as innovative as the all-rounders themselves.
A robot welding cell in a class of its own
A prime example of the state-of-the-art production technology at Arburg can be found in sheet metal production. This is where the machine stands for the injection moulding machines, which weigh tons, are produced in all conceivable designs. Wolfgang John, head of the non-cutting manufacturing department, sums up the special production engineering features: "Here we produce exclusively to customer order, which often means batch size 1 given the wide range and modularity of our injection moulding machines. For this we need a robot welding cell with maximum flexibility, where offline programming, maximum availability and process reliability as well as first-class welding results are indispensable."
The welding specialists from Yaskawa Europe made the running here. And what they have installed in close cooperation with the Arburg managers in Lossburg is impressive: A high-tech welding cell, approximately 11 meters long and 4.5 meters wide, is situated in a very confined space. A Motoman MA2010 six-axis robot is suspended from its X-Y-Z portal. Two special rotary positioners pick up the pre-worked, up to 5,500 millimeters long and three tons heavy machine stands using suitable jig carriers, which are then MAG gas shield welded by the welding robot in perfect trough position.
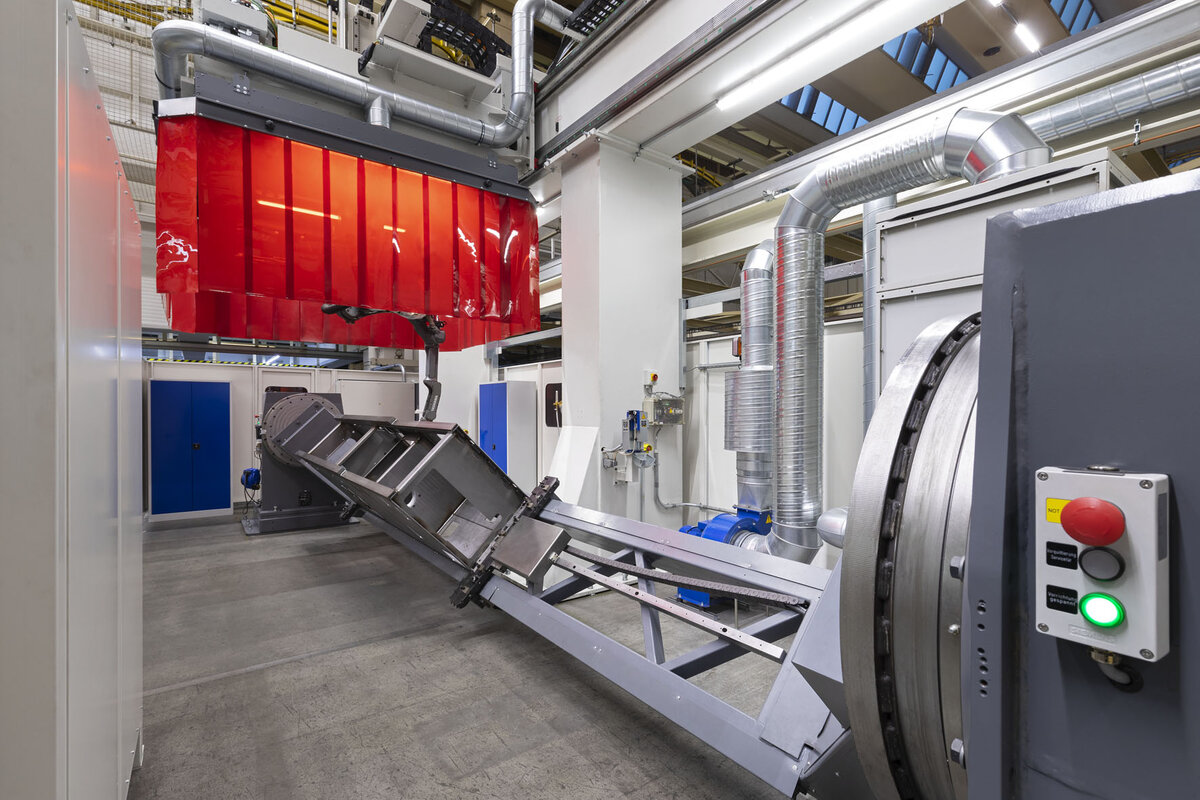
Up to 100 meters of weld seam per component
All machine stands are made of the sheet metal material S235, whereby the material thicknesses vary between five and eight millimetres depending on the model. A 500 ampere welding source by Lorch and a water-cooled welding torch in combination with the path-precise and dynamic Motoman robot guarantee high welding speeds and first-class seam quality: "We draw welds of up to 100 meters per component. Here we depend on efficiency and reproducible quality. The welding seams not only have to meet visual requirements, but also have to be permanently leak-proof, especially in the case of containers for hydraulic oil," says Wolfgang John.
In practice, one can only marvel at how dynamically the slim welding robot with its internal hose package does its work. Even in corners or tight radii, the MA2010 hardly needs to reduce its welding speed. Largely spatter-free welding shows how safely controlled the process is. The DX200 controller smoothly handles the synchronization of the total of eleven NC-controlled axes - six of the robot, three of the gantry and two of the positioner.
The lot size 1 challenge
However, the greatest challenge for the plant is the small batch sizes, which increasingly tend to be lot size 1. Nevertheless the company is well equipped to deal with unproductive set-up times, as Martin Braun, the Arburg Group Manager for Electrical Equipment Design, assures: "We consistently rely on the opportunities provided by offline programming. In addition, we have invested a great deal of creativity in the design of an intelligent fixture carrier with a highly flexible clamping system that allows us to securely clamp all machine stand variants simply within minutes. This is the only way we can meet the challenge of batch size 1."
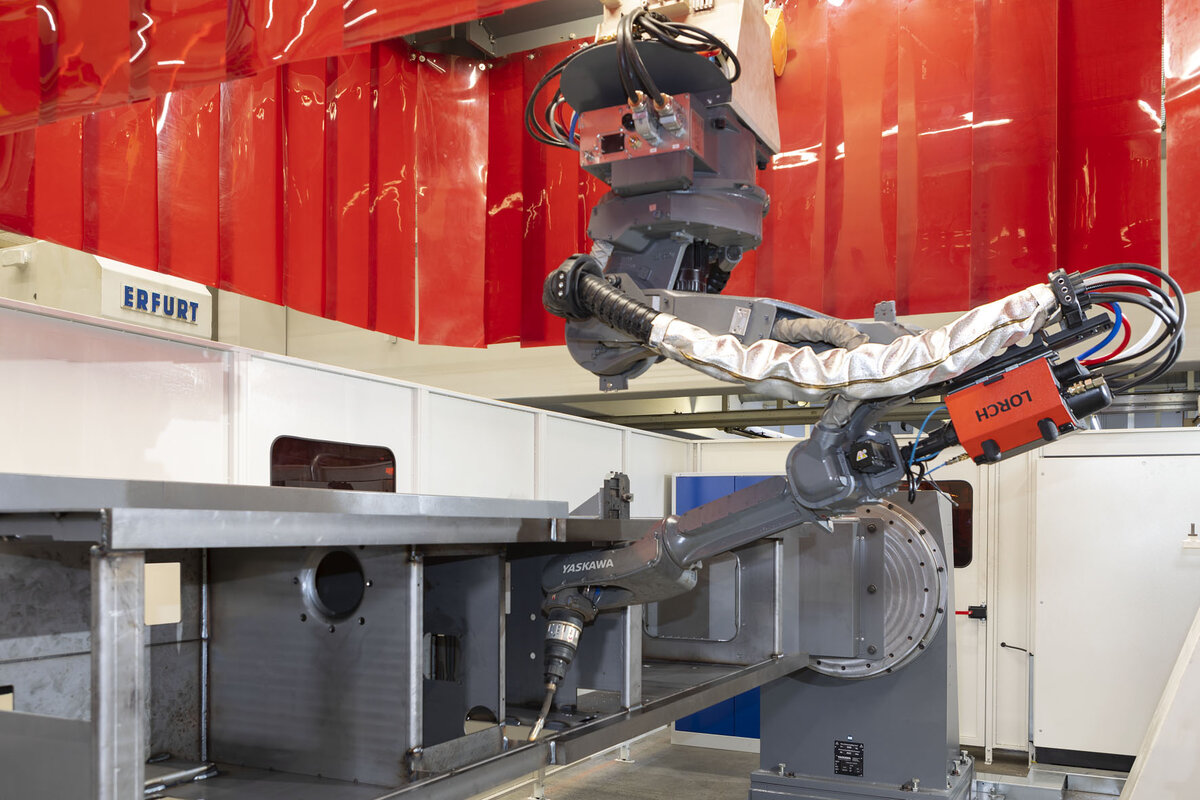
Offline programming makes the impossible possible
Arburg uses Yaskawa's MotoSim offline programming system for programming new components on the computer and the operators are very enthusiastic about the system. It permits designing a realistic 3D simulation by using the same kinematic model as the DX200 robot controller. The programming language is also identical, making it possible to completely develop welding programs offline. "With MotoSim we reduce the programming times considerably and limit the effort for final on-system teaching by about 80 to 85 percent", says Martin Braun.
At present, almost 100 machine stand variants are stored in the memory of the control system, more will follow. After the changeover from one component to the next, the operator only has to select the appropriate program and the robot carries out its welding program. In order to ensure the highest level of safety, the welding cell is equipped with a wide range of sensors and special measuring equipment to ensure system geometry. This means that each individual robot axis can be measured individually by approaching special calibration points and, of course, sensors monitor the secure clamping of components weighing several tons. Industry 4.0 at its best.
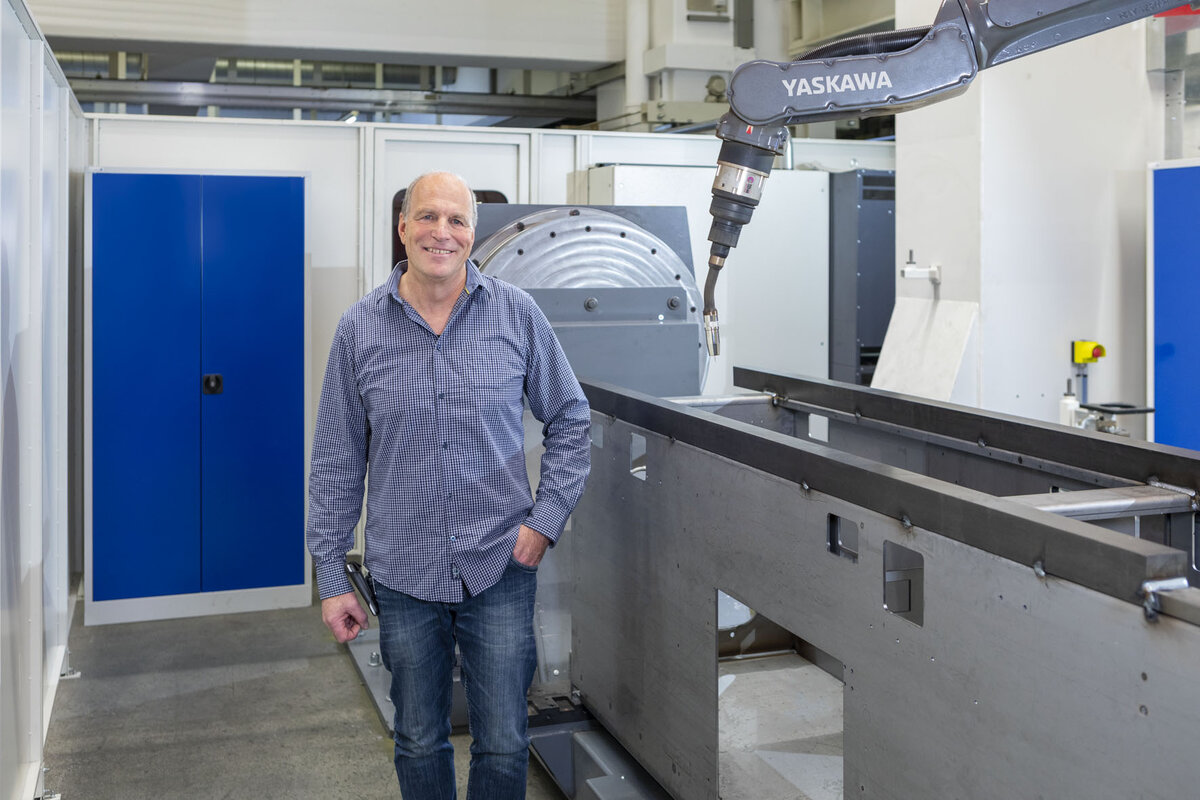
Cooperation and partnership as a factor for success
The know-how of the Arburg team, which has developed over decades, made a decisive contribution to the fast and uncomplicated commissioning of the plant. The specialists from the Black Forest with experience in robotics also get on very well with the welding cell during operation. And robots and components from the Japanese supplier are also renowned for their reliability. So it’s no surprise that the plant has been operating reliably since its commissioning in August 2019 and that it has met the high expectations.
Even though the demand for external services will remain manageable in the long term - Arburg has an excellent maintenance team - the Black Forest company is particularly keen to maintain a good relationship with its suppliers: "We have been using Yaskawa products for many years and value their quality. But we also know that we can rely on Yaskawa's support in an emergency. And that’s what counts," concludes Wolfgang John.
Text: Ralf Högel
Contact readers’ enquiries
Tel. +49-8166-90-0
Fax +49-8166-90-103